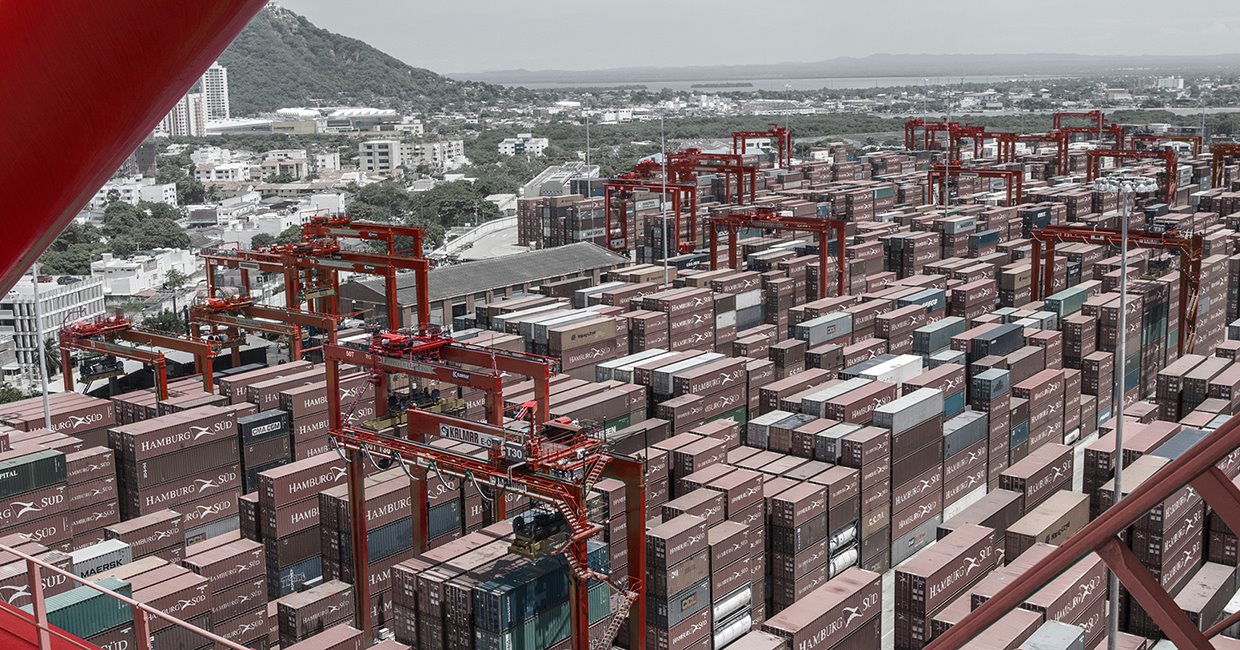
Sustainable terminal automation
A conversion to automation is a significant undertaking that requires deep technical expertise as well as a capacity to integrate numerous complex systems. In order to carry out the conversion in a sustainable way from the point of view of the environment, the economy and people, both client and vendor need to focus on careful mapping of the terminal’s business processes as well as on a deep-reaching change in operational culture. Successful automation conversion is about culture change as well as technology.
Co-authored by Ilkka Annala and Tommi Pettersson
Automation is widely accepted as the way towards improved productivity, safety, efficiency and competitiveness at today’s container ports and terminals. In addition to newly built greenfield terminals, the benefits of automation are also accessible to existing terminals.
Automated terminals can help improve the sustainability of operations in several ways. Optimised container flows reduce energy consumption and emissions. Automated equipment leads to a safer working environment, significantly lower accident rates and reduced insurance costs. Automated operation also extends equipment lifetimes, thus preserving resources and contributing to sustainability.
Cornerstones of success
Automation projects always revolve around a basic wish list – an idealised implementation that encompasses the following:
- Minimum operational downtime
- Shortest time to value
- Improving and maintaining operational performance
- Improving and maintaining reliability
Success in practice will depend on skilful optimisation of these and numerous other factors. A key consideration is implementation time. On one hand, terminals seek to minimise the cost of conversion, often by combining components from multiple vendors. On the other hand, every interface between two systems must be automated. The simpler the overall system and the fewer interfaces that need to be integrated and tested, the faster the implementation. Simply optimising for the cost of individual system components is a short-sighted approach. A delay of just a few weeks on a major automation project can cost millions of euros in terminal downtime.
If automation is built with a “bits and pieces” approach, the terminal may save in the very short run, but these savings can be lost already at the deployment stage due to the added complexity of integration. By contrast, a vendor that can offer a pre-integrated solution will be able to provide a system that is not only deployed faster, but is also more cost-effective as a whole.
Proven modules
Typically, several automated system suppliers will work on the same project. As a rule of thumb, every system needs at least one interface to another system, and someone has to integrate these interfaces. If the number of suppliers and systems is kept to a minimum, the number of different interfaces is also reduced dramatically. The system thus becomes simpler and faster to integrate.
In a standard project, integration is carried out by the terminal operator, a third-party consultant, or one of the automation suppliers. Some suppliers such as Kalmar can offer readily integrated solutions to most tasks in the terminal. Kalmar can also offer professional service support to customers who need a knowledgeable system integrator to work on their project.
Terminal automation is usually considered a project. However, a more fruitful approach would be to think in terms of proven modules
Each terminal is different and there is no single solution that fits all operators. A key conceptual point is that terminal automation is usually considered a project. However, a more fruitful approach would be to think in terms of proven modules – i.e. combinations of tested and standardised hardware and software components. This change in perspective helps shorten implementation times and improves the efficiency of the finished system, ultimately contributing to increased sustainability thanks to saved resources.
Maintaining peak capacity
One of the most important considerations in any automation conversion at brownfield terminals is how to ensure the highest possible capacity during the conversion project, while minimising disruption to terminal operations. Usually, this will require a step-by-step approach to the conversion.
For existing straddle carrier operations, the alternative routes are:
- Conversion to fully automated AutoStrad™ operation
- Adding stacking capacity by using some ASC blocks in the stacking area and handling the remaining terminal and ASC waterside horizontal transportation operation with existing manual straddle carriers. With this approach, the terminal can continue operation during the transition.
- Full ASC + automated shuttle carrier (AutoShuttle) conversion
For an existing RTG operation, the options are:
- Full ASC + AutoShuttle conversion
- Full or partial AutoRTG operation with horizontal transportation based on shuttle carriers or terminal tractors
The sustainability implications of automation conversion vary depending on the type of terminal. For example, converting an existing straddle carrier terminal to AutoStrad™ operation section by section might be the easiest from this perspective. The environmental impact of the conversion is minimal since the entire terminal infrastructure need not be rebuilt, with the exception of adding fences, safety systems, road interchange functions and navigation beacons for the straddle carriers.
With a minimal infrastructure impact, AutoStrad™ conversion offers rapid savings in operational and maintenance expenses. Energy consumption is noticeably reduced thanks to more efficient automated driving as well as a reduced need for yard lighting and air-conditioning. AutoStrad™ also save fuel by enabling engine stop and start functionality during idle periods, which is very hard to implement consistently with traditional manually driven straddle carriers.
Smooth and efficient deployment of new technology in an automation project requires thorough testing and pre-integration
Adding ASC blocks to a manual straddle carrier terminal also results in a fairly easy conversion, during which the manual terminal can continue its operation uninterrupted and the existing straddle carrier fleet can be used for waterside horizontal transportation.
Smooth and efficient deployment of new technology in an automation project requires thorough testing and pre-integration to ensure the compatibility of all systems. Kalmar can offer emulation of the company’s Terminal Logistic System (TLS) and various Terminal Operating Systems (TOS). The environment can be used for regression testing of new product releases.
Managing change
An easily overlooked aspect of terminal automation is that it is in fact more of a cultural than technical issue. Whether creating a new automated terminal or converting a manual terminal to automated operation, change management is crucial. Equipment upgrades are usually planned carefully, but people-related issues are quite often overlooked, even though human behaviour takes more time to adapt. Change is inevitable, so the question is how to manage it now.
Automation provides new job opportunities, but also places additional demands on the workforce
Successful change management requires an open dialogue with all stakeholders. Human resources need to be taken into account from the beginning. Automation provides new job opportunities, but also places additional demands on the workforce.
Furthermore, to be able to plan an efficient automated terminal, the terminal must be able to map all of its business processes. In automated terminals, what is not mapped cannot be automated.
Wanted: New skills
Automated operations require radically different skillsets compared to traditional terminals. Typical additional skills that are required include:
- Understanding the operating principles of automated equipment and systems
- Systematic planning of operation and maintenance work
- Data and fact-based usage and analysis compared to operators reporting faults in equipment
- Data mining
- Competence in measuring and sensor technology (that replaces the human senses)
New jobs that will need to be outsourced or insourced include automation system specialists; system optimisation engineers; IT system service and maintenance professionals; and instructors for internal staff and external parties. On the other hand, significantly fewer employees will be required for basic container operation and traditional maintenance tasks.
80% is not good enough
Manual systems will work even if they are not in perfect condition, since human operators can usually compensate for the quirks and deficiencies of each individual piece of equipment. To deliver their full potential, automated equipment and the entire system always need to be in 100% working condition.
This requires a major change in attitude for maintenance operations. The 75% to 80% equipment and system condition that is typically acceptable in manual equipment is simply no longer enough. Systematic pre-emptive maintenance processes become essential in automated terminals. However, as collisions and other accidents due to human error are eliminated, the need for ad hoc repairs is also reduced dramatically, bringing cost savings in the long term.
Towards a sustainable future
Automation is still very new in the port industry, compared to many other fields such as process industry, aviation, factory serial production and manufacturing. To evaluate the possibilities of increased sustainability due to automation, there is much that we can learn from other industries.
Successfully gaining knowledge and managing the transformation in a sustainable way is the key question for terminals seeking a competitive future
The long-term benefits of automation are clearly evident, but these benefits come with widespread changes that will need to be addressed in a comprehensive way. As warehouse workers have become operators of automated warehouses, and engine mechanics have become engineers who can calibrate integrated sensor systems, so will port workers need to become skilled professionals at home with sophisticated automated systems.
So far, a fairly limited amount of knowledge exists among port operators on how to operate and maintain automated systems efficiently. Successfully gaining this knowledge and managing the transformation in a sustainable way is the key question for ports and terminals seeking a competitive future.
This post is based on a Kalmar white paper on sustainable terminal automation.
DOWNLOADS
Related articles
Further reading
Subscribe and receive updates in your email
Subscribe