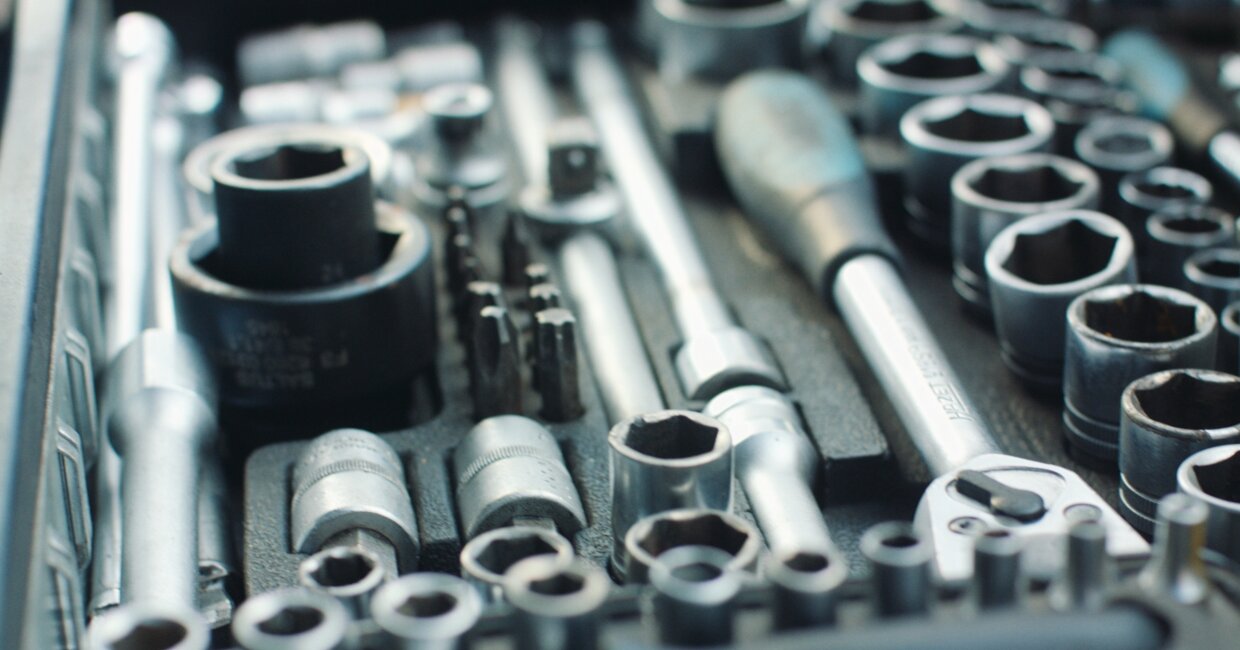
Taking the guesswork out of maintenance
Kalmar has made it easier for users of all types of equipment to keep on top of their maintenance schedules by developing an automated method of planning and coordinating maintenance work.
Preventive maintenance is one of the key elements of efficient equipment operation. Following maintenance schedules requires commitment by the customer, but the benefits in terms of productivity and safety are significant.
In some cases it will be clear when a replacement part or service is required, but issues that might reduce the performance of a machine – or even take it out of service - can be difficult to identify.
Undertaking maintenance work on time minimises the amount of time machines are out of operation, ensures that equipment remains operational for a period commensurate with its forecasted life expectancy and helps machines operate safely for both operators and other employees.
When a customer purchases new equipment they receive a hard copy of the maintenance manual, which includes information covering all aspects of the machine’s operation. Previously, the customer would then manually check when planned maintenance was scheduled, increasing the possibility of missing it and allowing machines to operate beyond the recommended maintenance interval.
“The automatic maintenance plan notifies the customer when each piece of equipment is within a specific period before its scheduled maintenance."
Digital planning improves maintenance management
The automatic maintenance plans available to customers who use Kalmar Insight complement these hard copy manuals. They provide these customers with an overview of the status of every machine, generating alerts when a scheduled maintenance is coming up and giving customers the opportunity to order the kit they need for each maintenance cycle.
Managing equipment maintenance becomes an increasingly complex and resource hungry process as the number of machines in operation increases, explains Hanna Kosunen, Senior Manager, Service Offering Kalmar.
“In many cases this process is based on someone manually checking how many hours each machine has operated since its last maintenance and relaying this information to the person responsible for maintenance,” she says.
With a manual process, when a piece of equipment nears its next scheduled maintenance the person responsible for maintenance would have to check the maintenance manual to find out what parts are required and if the company has these parts in stock before ordering.
Automatic maintenance plans reduce complexity
Further complications arise where the customer has many different pieces of equipment, each with different maintenance schedules.
“The automatic maintenance plan notifies the customer when each piece of equipment is within a specific period before its scheduled maintenance,” says Kosunen. “This notification is generated through Kalmar Insight, our cloud-based analytical tool that aggregates operational business data from equipment fleet, terminal operating and maintenance management systems.”
This proactive maintenance scheduling can also be applied to equipment from other vendors, giving customers complete visibility across their entire fleet.
“Even customers who take a proactive approach to maintenance scheduling can benefit from receiving notification of which kit they need to perform the next scheduled maintenance so they know exactly what to order and how to order it,” concludes Kosunen.
Related articles
Subscribe and receive updates in your email
Subscribe