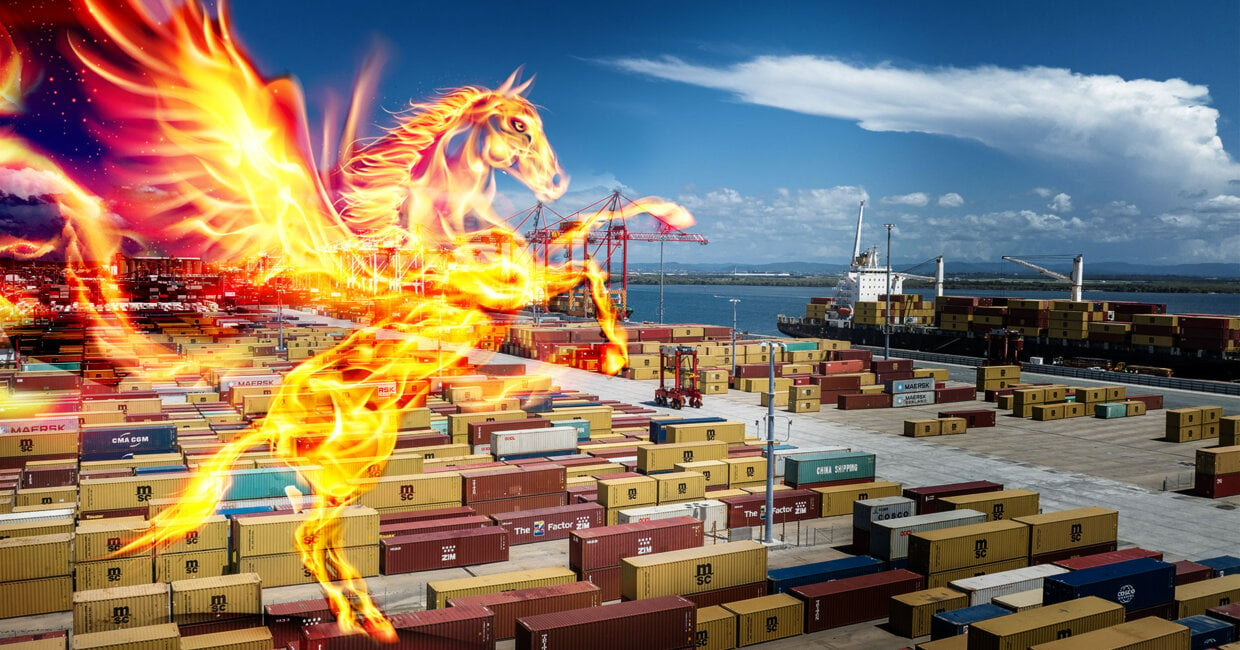
Myth #4: Automated yard operations require super advanced quay cranes
There is a general assumption that automated terminals require particularly complex ship-to-shore cranes. At least for Kalmar AutoStrad™, the opposite is in fact true. Kalmar automated straddle carriers only require a basic level of crane instrumentation and once this is in place, automated straddle carriers are much more flexible than automated guided vehicles (AGVs) in how they operate with the crane.
Most obviously, automated straddle carriers eliminate the need for dual-trolley STS cranes. Unlike AGVs, Kalmar automated straddle carriers can pick up and place containers directly on the ground, so they do not require the two-stage operation that is standard at quays served by AGVs, in which the secondary trolley of the STS handles the loading and unloading of the horizontal transportation equipment.
Dual-trolley cranes are significantly heavier, more expensive and more complex to maintain than their single-trolley counterparts. If a terminal is already equipped with this type of crane, automated straddle carriers can certainly operate with them, but they are not a requirement. AutoStrad™ can serve any type of quay crane as long as it is fitted with the instrumentation that provides information on the position and movements of the STS crane to the automation system. This means that when automating with Kalmar automated straddle carriers, the STS cranes do not need to be replaced.
Utilising the portal
Another key advantage of automated straddle carriers is that they are not limited to operating in the backreach area of the ship-to-shore crane. Kalmar automated straddle carriers can work in the portal area between the landside and waterside legs of the crane, in the same way as manual straddle carriers. The overall traffic flow must of course be planned, but the concept is perfectly realisable with automated straddle carriers. The location of hatch covers on the quay is introduced into the automation system, so the AutoStrad™ system is aware of them when making routing decisions.
Using the portal area for container transfers offers numerous benefits. The most immediate of these is that STS crane cycle times are much faster, as the trolley has a shorter distance to travel. Making use of the portal area also multiplies the number of transfer lanes available to the crane, thus significantly increasing the size of the container buffer.
As the straddle carrier concept enables completely decoupled operations, the quay crane can always operate at maximum capacity while automated straddle carriers handle the containers in the transfer lanes. The most practical option is typically to use the backreach area for storing hatch covers and focusing the container operations in the portal area next to the vessel. Using the portal area for container exchange also maximises the utilisation of the yard area, as the apron between the quay and container stacks can be narrower than in AGV operation.
At crowded quays with multiple STS cranes operating "bumper-to-bumper", container and hatch cover placement can be varied between cranes, with some cranes exchanging containers primarily under the portal and others utilising the backreach area. This is often the best option for optimising the traffic flow along the entire quayside. As automated straddle carriers do not have a driver onboard, operating under a suspended load is not a safety issue and opens more flexibility to the STS crane operation.
Kalmar automated straddle carriers can also support STS cranes with tandem spreaders, and especially discharging happens very fast as the STS crane can land two containers on the ground at once. With AGVs and dual-trolley cranes, tandem handling is a much more complex and therefore vulnerable process, since the secondary trolley needs to make two cycles for every one of the main trolley.
To summarise, automated straddle carriers are very flexible about the type of quay crane they serve. They can easily interface with both single-trolley and dual-trolley cranes, bringing shorter STS cycle times and more efficient buffering to either. The ability to pick and place containers on the ground frees the crane and horizontal transportation from the need to wait for each other, enabling optimum throughput and performance for the entire terminal.
Related articles
Further reading
Subscribe and receive updates in your email
Subscribe